Franse sonenergie-instituut INES het nuwe PV-modules ontwikkel met termoplastiek en natuurlike vesels wat in Europa verkry word, soos vlas en basalt.Die wetenskaplikes beoog om die omgewingsvoetspoor en gewig van sonpanele te verminder, terwyl herwinning verbeter word.
’n Herwinde glaspaneel aan die voorkant en ’n linne-samestelling aan die agterkant
Beeld: GD
Van pv tydskrif Frankryk
Navorsers by Frankryk se Nasionale Sonenergie-instituut (INES) – ’n afdeling van die Franse Kommissie vir Alternatiewe Energie en Atoomenergie (CEA) – ontwikkel sonkragmodules met nuwe bio-gebaseerde materiale aan die voor- en agterkant.
"Aangesien die koolstofvoetspoor en die lewensiklusontleding nou noodsaaklike kriteria in die keuse van fotovoltaïese panele geword het, sal die verkryging van materiale 'n deurslaggewende element in Europa word in die volgende paar jaar," sê Anis Fouini, die direkteur van CEA-INES , in 'n onderhoud met pv tydskrif France.
Aude Derrier, die navorsingsprojek se koördineerder, het gesê haar kollegas het gekyk na die verskillende materiale wat reeds bestaan, om een te vind wat modulevervaardigers kan toelaat om panele te vervaardig wat werkverrigting, duursaamheid en koste verbeter, terwyl die omgewingsimpak verlaag word.Die eerste demonstreerder bestaan uit heterojunction (HTJ) sonselle wat in 'n geheel saamgestelde materiaal geïntegreer is.
"Die voorkant is gemaak van 'n veselglas-gevulde polimeer, wat deursigtigheid bied," het Derrier gesê."Die agterkant is gemaak van saamgestelde materiaal gebaseer op termoplastiek waarin 'n weef van twee vesels, vlas en basalt, geïntegreer is, wat meganiese sterkte, maar ook beter weerstand teen humiditeit sal bied."
Die vlas is afkomstig van Noord-Frankryk, waar die hele industriële ekosisteem reeds teenwoordig is.Die basalt word elders in Europa verkry en word deur 'n industriële vennoot van INES geweef.Dit het die koolstofvoetspoor met 75 gram CO2 per watt verminder, in vergelyking met 'n verwysingsmodule van dieselfde krag.Die gewig is ook geoptimaliseer en is minder as 5 kilogram per vierkante meter.
"Hierdie module is gemik op die dak-PV en gebou-integrasie," het Derrier gesê.“Die voordeel is dat dit natuurlik swart van kleur is, sonder dat 'n agterblad nodig is.Wat herwinning betref, is die skeiding van die lae, danksy termoplastiek, wat hersmelt kan word, ook tegnies eenvoudiger.”
Die module kan gemaak word sonder om huidige prosesse aan te pas.Derrier het gesê die idee is om die tegnologie aan vervaardigers oor te dra, sonder bykomende belegging.
"Die enigste noodsaaklikheid is om vrieskaste te hê om die materiaal te stoor en nie om die hars-kruiskoppelingsproses te begin nie, maar die meeste vervaardigers gebruik vandag prepreg en is reeds hiervoor toegerus," het sy gesê.
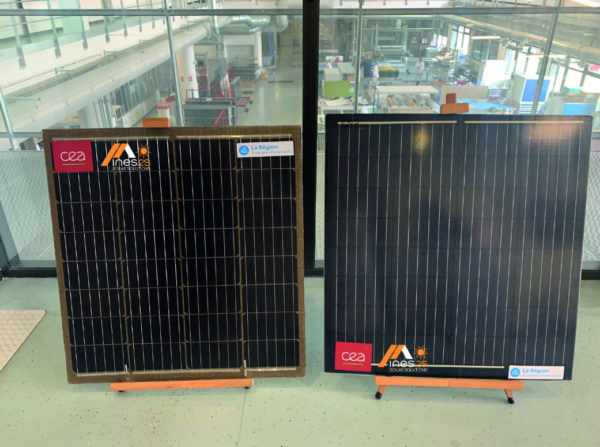
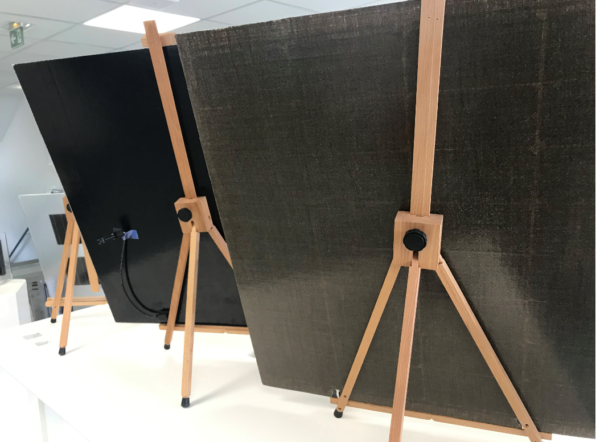
"Ons het aan die tweede lewe van glas gewerk en 'n module ontwikkel wat bestaan uit hergebruikte 2,8 mm-glas wat uit 'n ou module kom," het Derrier gesê."Ons het ook 'n termoplastiese omhulsel gebruik wat nie kruisbinding benodig nie, wat dus maklik sal wees om te herwin, en 'n termoplastiese saamgestelde met vlasvesel vir weerstand."
Die basaltvrye agterkant van die module het 'n natuurlike linnekleur, wat byvoorbeeld esteties interessant kan wees vir argitekte in terme van fasade-integrasie.Daarbenewens het die INES-berekeningsinstrument 'n 10%-vermindering in die koolstofvoetspoor getoon.
"Dit is nou noodsaaklik om die fotovoltaïese voorsieningskettings te bevraagteken," het Jouini gesê.“Met die hulp van die Rhône-Alpes-streek binne die raamwerk van die Internasionale Ontwikkelingsplan het ons dus na spelers buite die sonkragsektor gaan soek om nuwe termoplastiek en nuwe vesels te vind.Ons het ook gedink aan die huidige lamineringsproses, wat baie energie-intensief is.”
Tussen die druk-, pers- en afkoelfase duur die laminering gewoonlik tussen 30 en 35 minute, met 'n werkstemperatuur van ongeveer 150 C tot 160 C.
"Maar vir modules wat toenemend eko-ontwerpte materiale insluit, is dit nodig om termoplastiek teen ongeveer 200 C tot 250 C te transformeer, met die wete dat HTJ-tegnologie sensitief is vir hitte en nie 200 C moet oorskry nie," het Derrier gesê.
Die navorsingsinstituut werk saam met Frankryk-gebaseerde induksie-termokompressiespesialis Roctool, om siklustye te verminder en vorms te maak volgens die behoeftes van kliënte.Saam het hulle 'n module ontwikkel met 'n agterkant van polipropileen-tipe termoplastiese saamgestelde, waarby herwonne koolstofvesels geïntegreer is.Die voorkant is gemaak van termoplastiek en veselglas.
"Roctool se induksie-termokompressieproses maak dit moontlik om die twee voor- en agterplate vinnig te verhit, sonder om 200 C by die kern van die HTJ-selle te bereik," het Derrier gesê.
Die maatskappy beweer die belegging is laer en die proses kan 'n siklustyd van net 'n paar minute behaal, terwyl minder energie gebruik word.Die tegnologie is gemik op saamgestelde vervaardigers, om hulle die moontlikheid te gee om onderdele van verskillende vorms en groottes te vervaardig, terwyl ligter en duursame materiale geïntegreer word.
Pos tyd: Jun-24-2022